In order to be able to correctly mill any type of object made with RealGUIDE, then surgical templates/guides or prosthetic reconstructions, objects created with the Sandbox, etc., it is necessary to set essential parameters so that the part in contact with the preparation or the model fits perfectly on it. Without the use of these parameters for milling ANY type of restoration will never fit perfectly on its model. So if you have problems with the fit and fitting of surgical templates/guides or prosthetic reconstructions, etc. on the relevant working models, surely one of the first checks to be made is on this phase of the design.
MILLING PARAMETERS FOR SURGICAL TEMPLATES/GUIDES CREATED IN THE REALGUIDE DESIGN MODULE:
The milling parameters are present in the design phase of the model on which the template/surgical guide is to be built, it must be unloaded, i.e. free of undercuts.
It must be compensated for in areas where the diameter of the surface of the anatomy model is smaller than the diameter of the milling cutter used to mill the internal area of the template, otherwise there would be material left over because the tool would not have enough space to remove it, hence the need to "compensate" the surface of the model, in the case of milling the template/surgical guide only.
If the template/surgical guide is made by 3D printing, obviously such parameters should not be entered.
Normally such parameters for the realisation of surgical templates/guides are deactivated as can be seen from the following image :
Not activating these parameters results in the undercuts only being unloaded onto the model intended for the construction of the surgical template/guide:
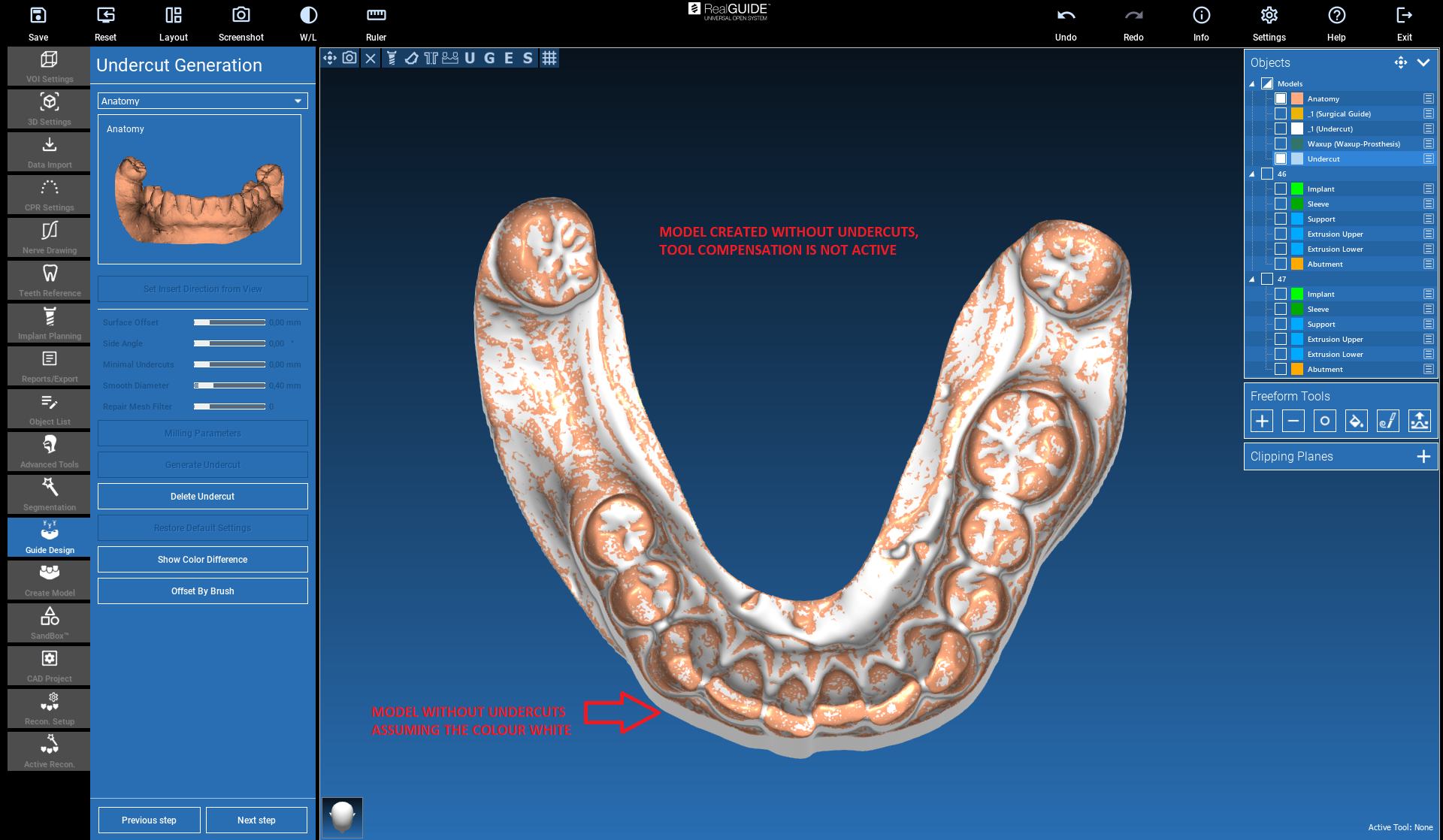
The parameters are activated by clicking on the "Milling parameters" icon; once the available menu is open, activate the "Anticipate milling" function and enter the milling cutter diameter used for milling the internal part of the template/surgical guide. We recommend entering a slight tolerance with respect to the nominal diameter of the milling cutter, so if a 1 mm milling cutter is declared, enter a value of 1.04/1.06, etc. mm. This is to avoid creating cavities that are too precise, as this could create problems as the milling operation must always establish the path of the tool centre of the cutter, which deviates from the contour of the piece to be milled by a distance equal to the radius of the cutter. Therefore, when milling a contour defined by curves, even complex ones, it is necessary to program the path of the cutter centre in relation to the radius of the tool used, leaving this slight tolerance as the cutter may not be able to remove all the material, or may even break:
The subtraction of the milling will create a compensated model surface, as can be seen from the following image, in the areas where the cutter diameter would not have been able to pass; at this point the undercuts are blocked and the compensated model that the software proposes is white:
Another function the software provides is the option to compensate for bullnose or flat cutters:
The 'Bullnose/Flat milling cutter' option allows you to enter the diameter of the tool used in the milling process and to enter the 'flat percentage' of the cutter. So for the sake of argument, if we enter a milling cutter diameter of 1 mm and a flat percentage value of 100%, we will have a perfectly Flat tool. If we enter a milling cutter diameter of 1 mm and a flat percentage value of 80%, we will have a Bullnose tool:
you can then proceed to the design of the template/surgical guide, its export and milling.
MILLING PARAMETERS FOR RECONSTRUCTIONS CREATED IN THE REALGUIDE CAD MODULE:
The milling parameters are present in the design phase of the model on which the reconstruction is to be built; it must be created without undercuts.
It must be compensated for in areas where the diameter of the surface of the anatomy model is smaller than the diameter of the milling cutter used to mill the inner area of the reconstruction, otherwise material would remain because the tool would not have enough space to remove it, hence the need to "compensate" the surface of the model, in the case of milling the reconstruction only.
If the reconstruction is realised by 3D printing, obviously such parameters should not be entered.
Normally such parameters for the realisation of reconstructions are active as can be seen from the following image :
Failure to activate these parameters results in only the undercuts being unloaded onto the model for reconstruction construction:
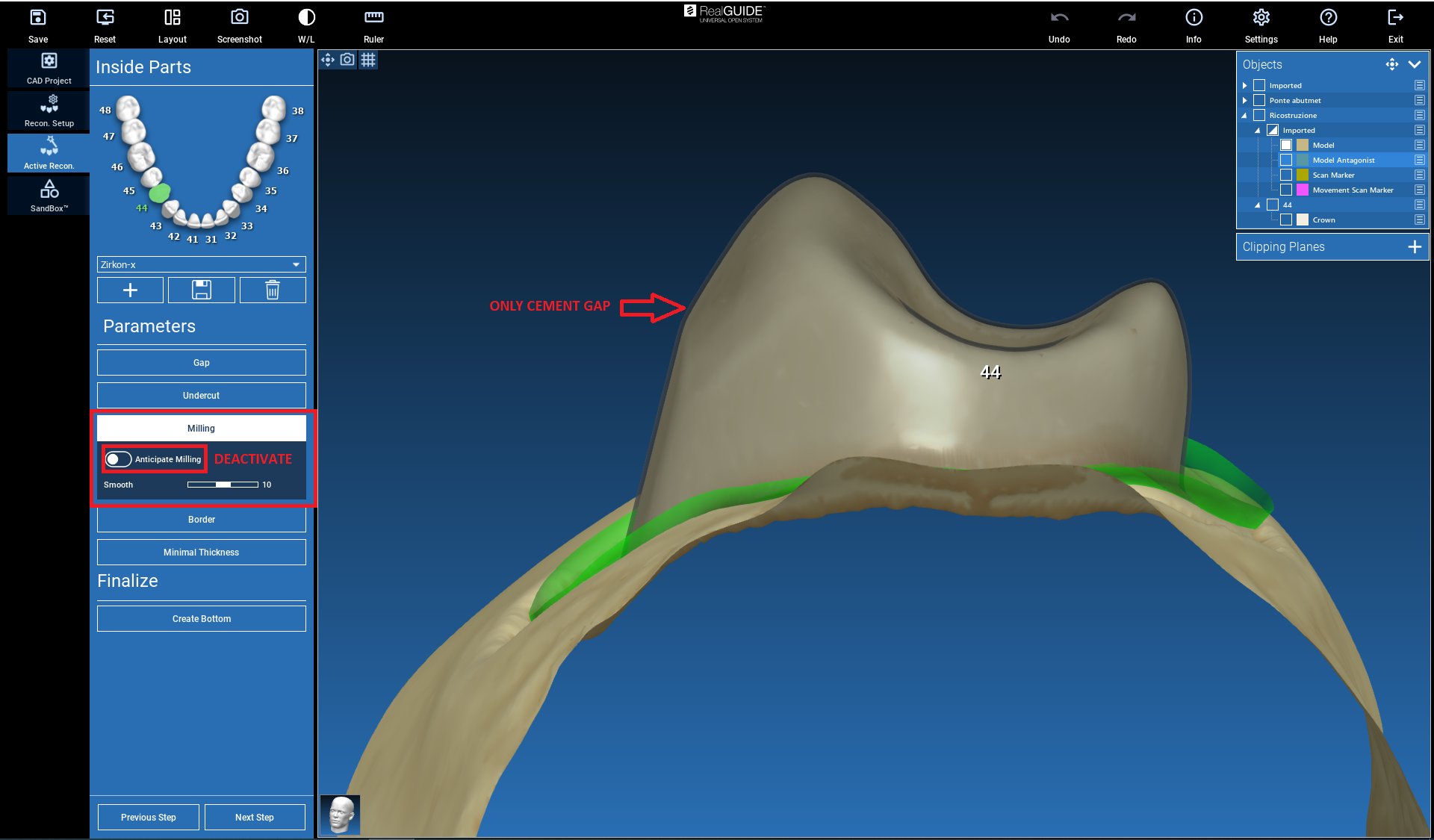
The parameters in the "Milling" section are activated by activating the "Anticipate milling" function. Here you enter the milling cutter diameter used for milling the inner part of the reconstruction. We recommend entering a slight tolerance with respect to the nominal diameter of the milling cutter, so if a 1 mm milling cutter is declared, enter a value of 1.04/1.06, etc. mm. This is to avoid creating cavities that are too precise, as this could create problems as the milling operation must always establish the path of the tool centre of the cutter, which deviates from the contour of the part to be milled by a distance equal to the radius of the cutter. Therefore, when milling a contour defined by curves, even complex ones, it is necessary to program the path of the cutter centre in relation to the radius of the tool used, leaving this slight tolerance as the cutter may not be able to remove all the material, or may even break. The tool compensation will create a compensated internal surface of the reconstructions as can be seen from the following image, in areas where the diameter of the cutter would not have been able to pass for the complete milling of this area:
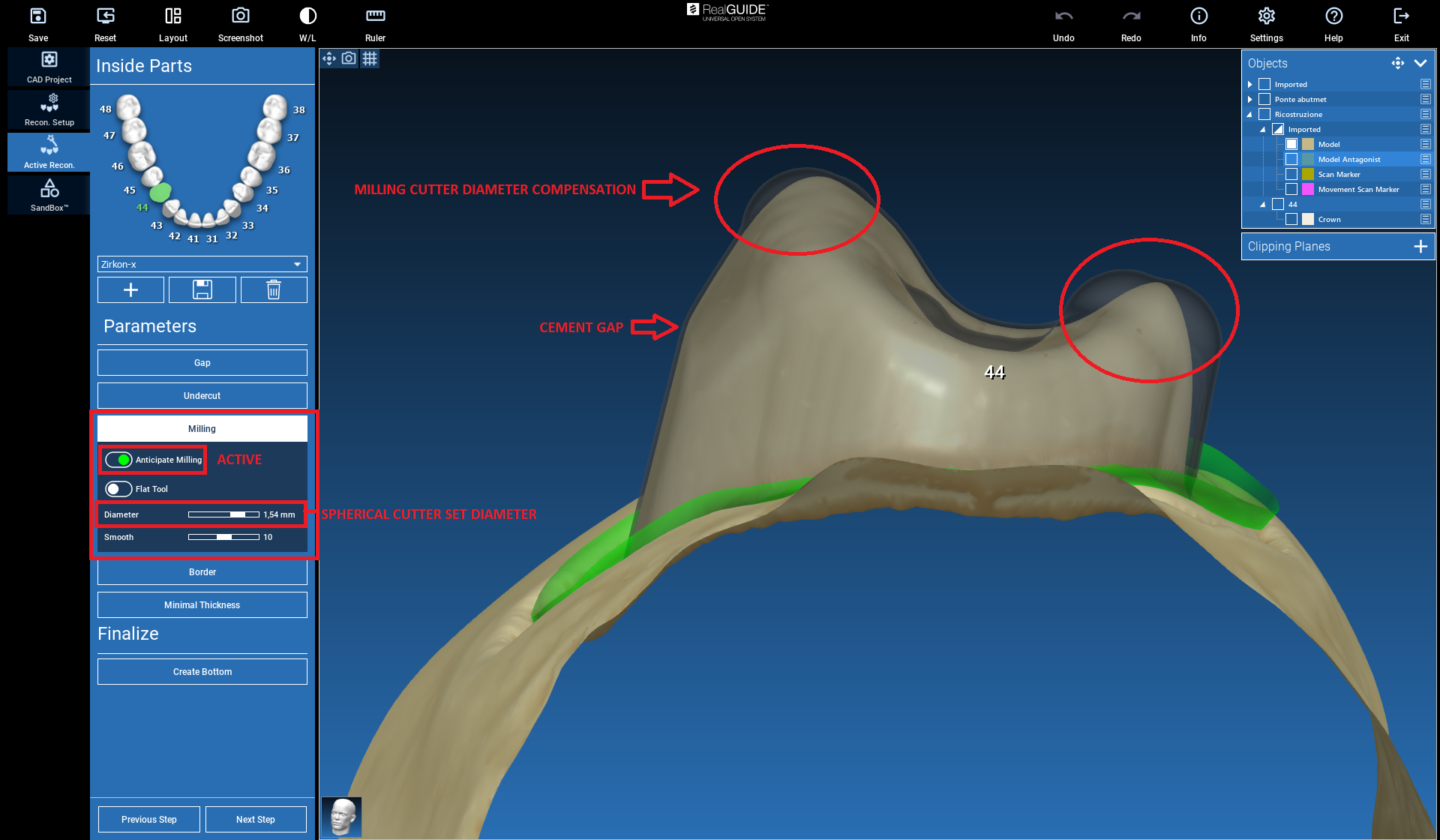
Another function the software provides is the option to compensate for bullnose or flat cutters:
The 'Bullnose/Flat milling cutter' option allows you to enter the diameter of the tool used in the milling process and to enter the 'flat percentage' of the cutter. So for the sake of argument, if we enter a milling cutter diameter of 1 mm and a flat percentage value of 100%, we will have a perfectly Flat tool. If we enter a milling cutter diameter of 1 mm and a flat percentage value of 80%, we will have a Bullnose tool:
you can then proceed with the design of the reconstruction, its export and milling.